The LT40 Sawmill History: Engine Upgrades
Tags
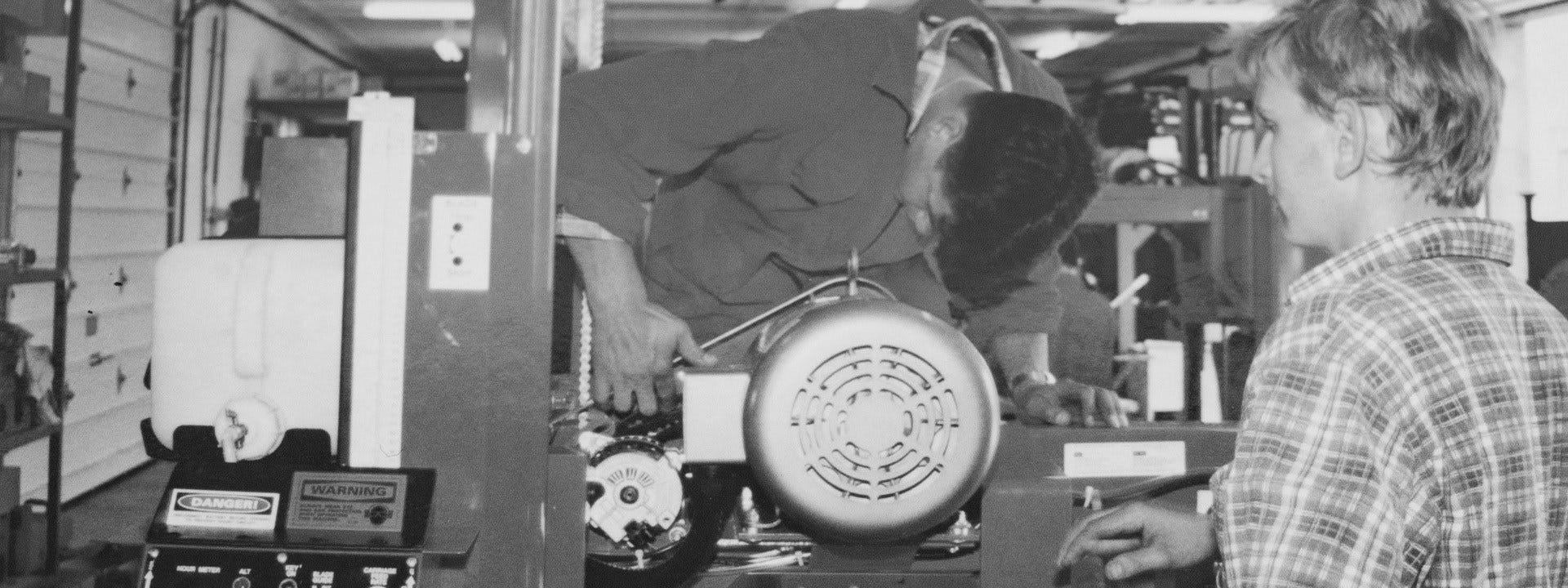
The sawmill’s engine is one of the most critical components in generating the necessary power for efficient sawing. The engines installed in the first LT40 sawmills at the beginning of the 1990s were economical and relatively strong. Still, most importantly, they were a perfect match for a portable sawmill's lightweight and compact construction. The LT40 sawmill, equipped with an easy-to-operate and strong engine, established a new direction in building sawmills outclassing the heavy, clumsy and inefficient stationary frame sawmills used in the industry at the time.
A typical sawmilling company from the late 1980s operated on a heavy and outdated stationary frame sawmill, which resulted in inefficient timber production. It generated high economic costs and negatively impacted the natural environment. The engines used at that time consumed a great deal of energy, and their work was also wasted on producing more woodchips and sawdust with thicker sawmill blades. These motors were mainly electric, oversized, with the characteristic cooling ribbing, making them seem powerful, but in fact, they had relatively low power concerning their impressive sizes.
Only with the engines installed in the LT40 sawmill came a tremendous change and showed a new direction. Despite their small size, they generated enough power, didn’t consume much fuel, and were easy to operate. It was an ideal match for the lightweight and compact construction of the portable sawmill designed for converting logs to lumber in any location. With a proper engine producing enough horsepower, a thin, narrow sawmill blade could easily make boards with a flat surface. It didn’t matter if it was hardwood, a large-diameter log, or the operator working on a sawmill in a harsh climate.
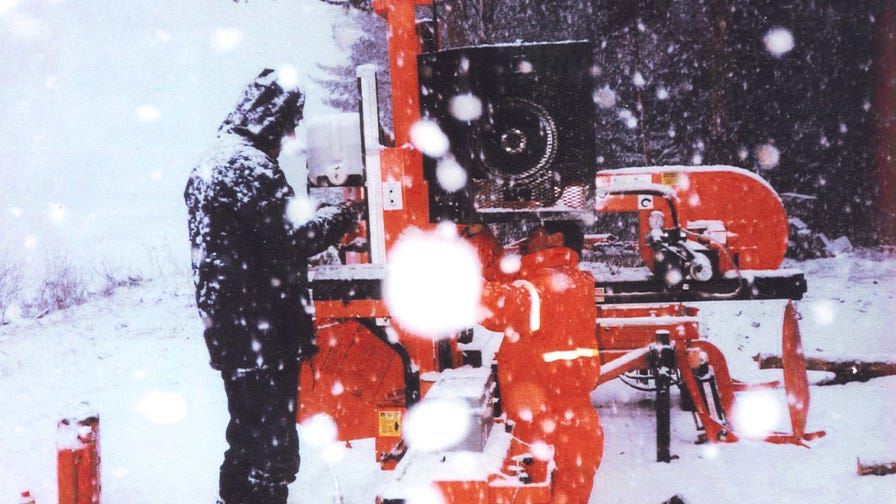
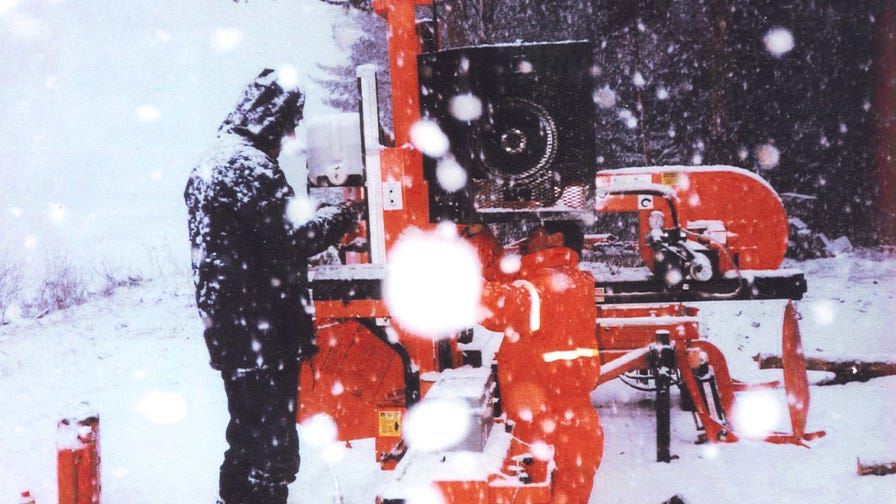
Combustion engines in the LT40 sawmill
The first LT40 sawmills that came to Poland in the 1990s were installed with gasoline engines supplied by the American company ONAN. It was a 2-cylinder boxer engine with a big cast-iron flywheel, generating 24 HP. The engine was said to be sturdy and reliable – it was simple in construction and operation and worked well in all weather conditions.
In 1992 the offering was extended by the first diesel engine from ACME Motori. This Italian unit generated 20 HP; however, it didn’t win much user approval. „The engines from ACME Motori perhaps looked nice and were compact but didn’t do well in the sawmills. They were designed mostly for building machineries, such as electrical generators or plastering machines, where they worked stably and continuously. In a sawmill, that engine worked well at a low speed, but once the blade got engaged and the engine started to work under the load, it lost its even and stable rhythm of work,” explains Robert Fret, an experienced Customer Service Specialist.
The range of combustion engines expanded in 1996 with the introduction of an Italian diesel engine Lombardini, available in two versions - 30 HP and 40 HP. This engine required more attention and care during the operation and didn’t appeal to customers. Its main weakness was frequent overheating of the head and a malfunctioning fuel injection system.
In 2000, the Wood-Mizer sawmills received the Japanese diesel engines from Kubota, quickly gaining popularity among the users. These engines were simple in construction, reliable, and worked flawlessly in almost every climatic environment. The camshaft was built on cogwheels which released the owners from remembering about its service. „When we introduced the Kubota engines to the offering, all our problems with the main unit disappeared. For the past 20 years, I can recall just two major breakdowns of this engine that were reported to our department,” says Dariusz Kujawa, the Customer Service Manager who has been with Wood-Mizer since the early 1990s. Due to the high emission standards, the Kubota D33 and D42 engines are no longer in Europe. For the past several years, the dominant engine in the LT40 sawmill has been supplied by Kohler, the manufacturer of well-proven and reliable gasoline engines.
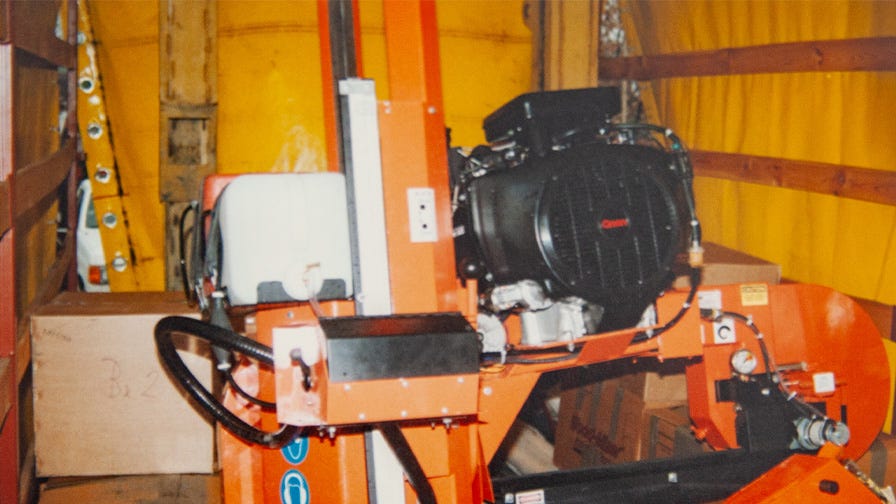
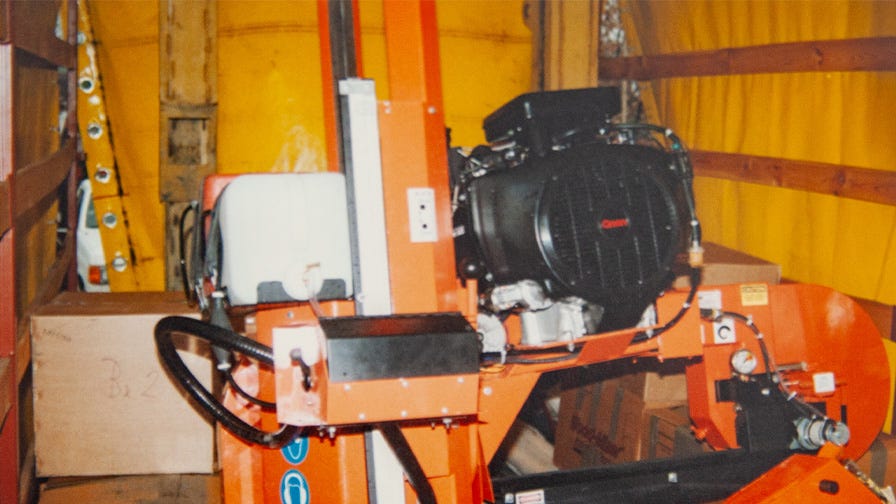
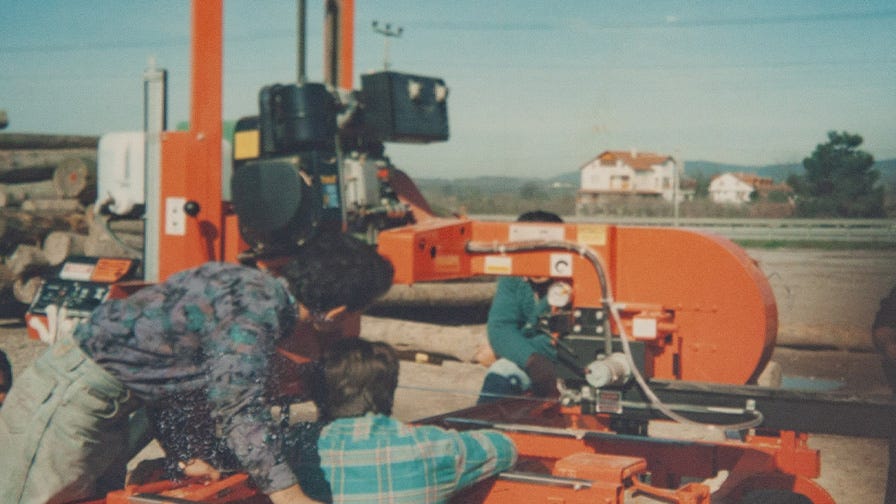
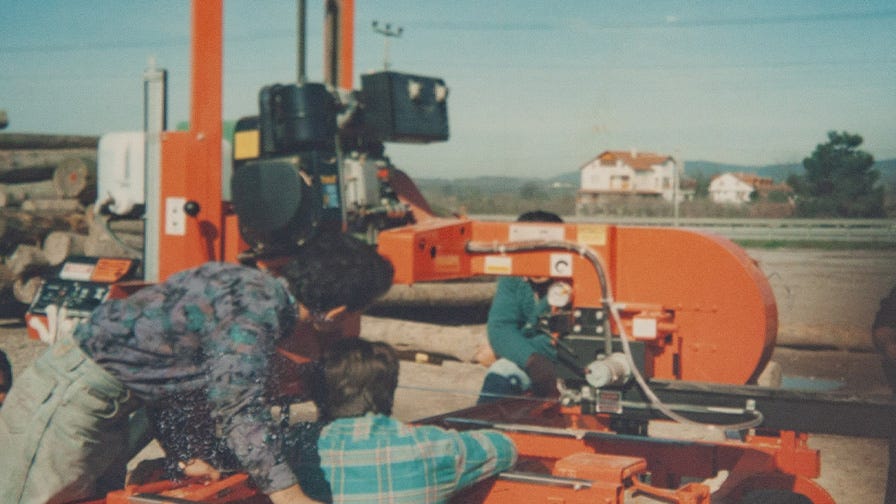
Electric motors in the LT40 sawmill
The first electric motors in the LT40 sawmill for the European market arrived in 1991 and were gradually becoming increasingly popular among users. The American Baldor (11 kW) engines with a classical starter mechanism had the reputation of being durable and reliable units, relatively strong compared to their small size. „The first electric motors from Baldor made an impression on our customers. They were lightweight and compact, with a smooth main block without any ribbing. People couldn’t believe that such a small motor could generate so much power,” recalls Robert Fret.
The LT40 sawmill from the early 1990s with a 3-phase electric motor was coupled with a 12V DC installation used for powering the sawhead feeding mechanism and the hydraulic functions of the bed. In practice, it meant that even though the sawmill was equipped with the AC main motor, it also needed a 12V battery and an alternator for charging it. „It raised much controversy among our customers because they couldn’t quite understand why a sawmill with the main electric motor needed an alternator additionally,” says Robert Fret.
In the LT40 sawmills from the beginning of the 90s, the base plate for the engine was universal, allowing the owner to have the main engine switched from gasoline to the electric one if he decided it would bring him additional savings. It was a common practice then to change the central unit from gas to electric (or the other way round, depending on the needs), and Customer Service employees often did it for the users. The entire operation of swapping the main engine took just two hours and eventually could be done individually by the sawmill owner.
A complete transition to the AC power supply in the LT40 took place only in 1998 and was a very significant technical upgrade of the sawmill. This modification allowed for a unified 380V electrical installation without an alternator and a battery. The new installation improved the operation of the hydraulic functions of the bed and qualified for introducing new functions. In the AC versions of the LT40 sawmill, it was not necessary to grease the connectors in the drum switches, which was a requirement in the DC versions – it was an efficient modification from the operator’s point of view.
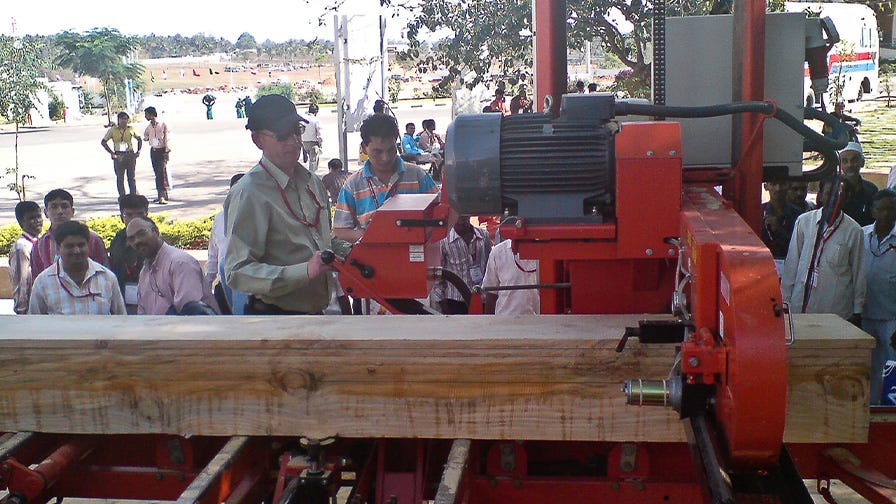
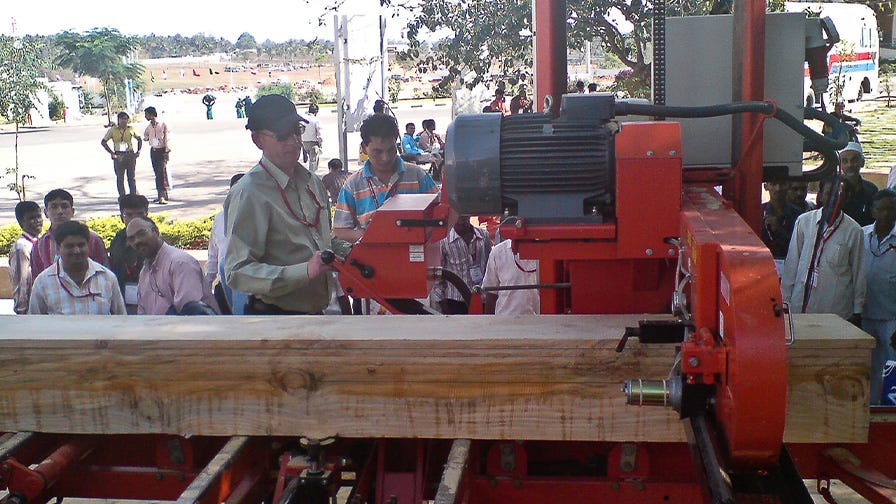
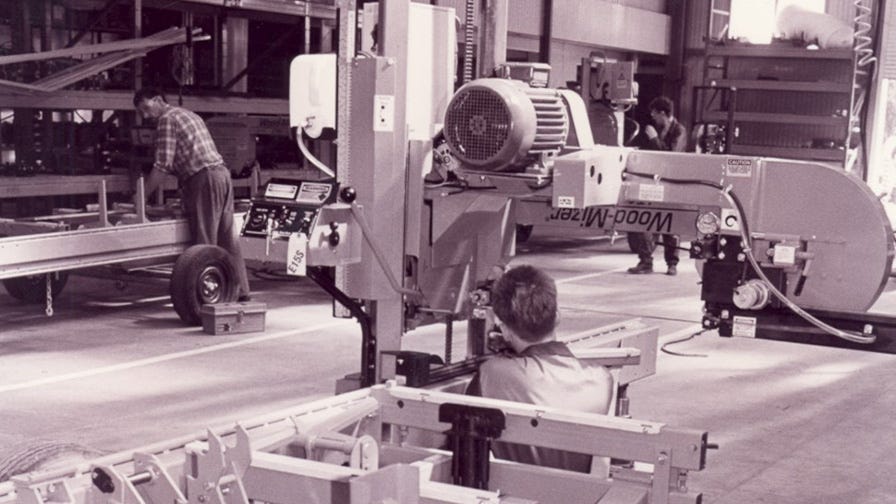
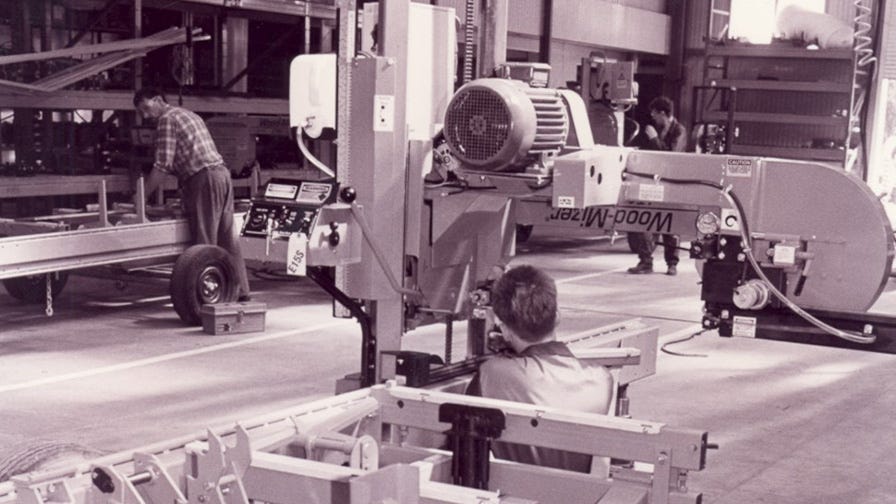
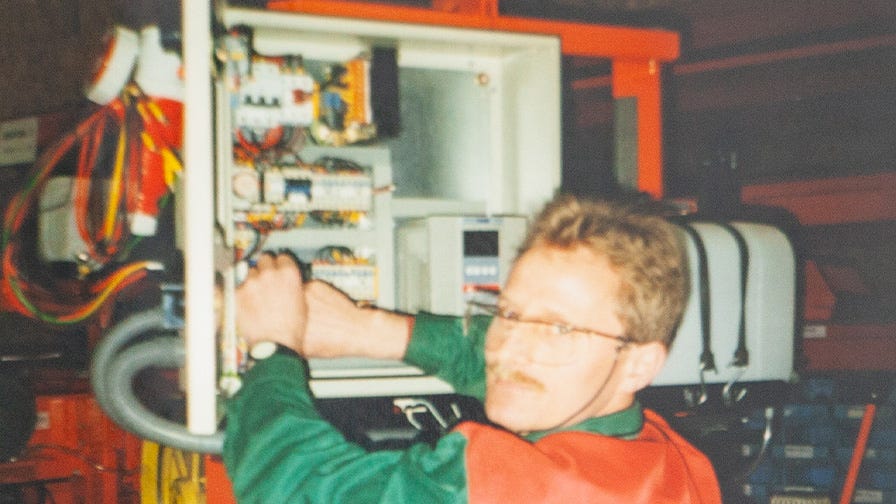
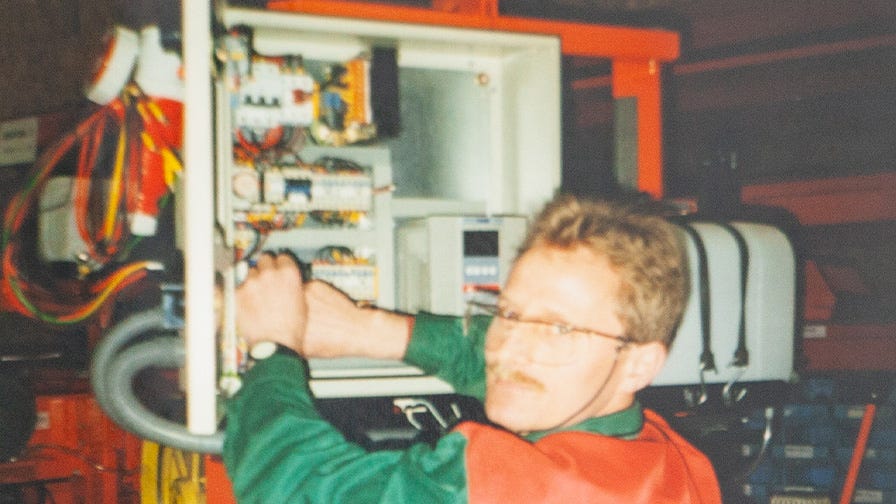
Who needs a gasoline engine, and who needs an electric motor?
Although the first LT40 sawmills built in the USA were equipped with gas engines, the electric motor was more appealing to customers in some European countries. The basic engineering assumption of the LT40 sawmill’s inventors Don Laskowski and Dan Tekulve, was to create a light and compact machine which would allow for cutting wood in any place around, so the idea of employing a combustion engine was very much justified. Additionally, the geographical distances in the USA are more significant than in Europe, the population density in towns and villages is different, and gasoline prices were more reasonable.
However, the situation in some European countries (e.g., Poland) was different. The sawmills users often worked close by the households where they could extend the electric cables and “borrow” some electricity from neighbors. The Baldor electric motor was known for its simple construction and minimal maintenance, unlike a gasoline engine which needed a seasonal change of oil and filters. Many customers decided to purchase a mobile LT40 sawmill with the electric motor bearing in mind that they would have to carry power supply cables wherever they wanted to go.
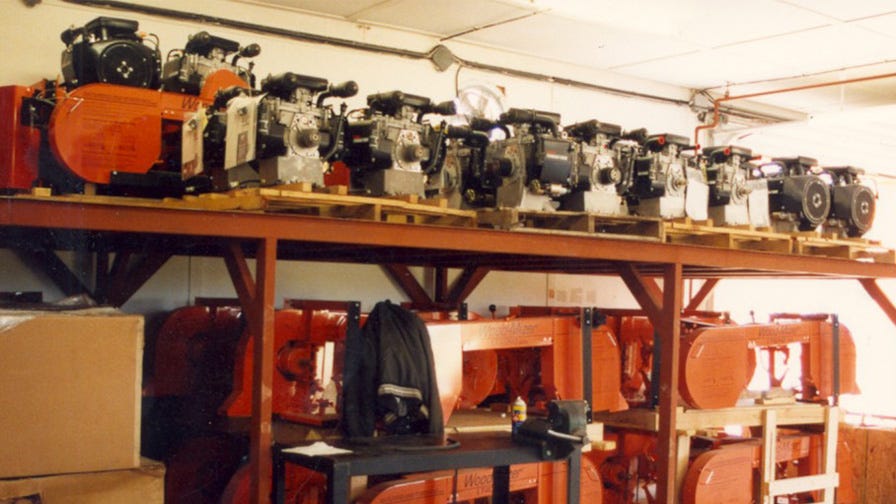
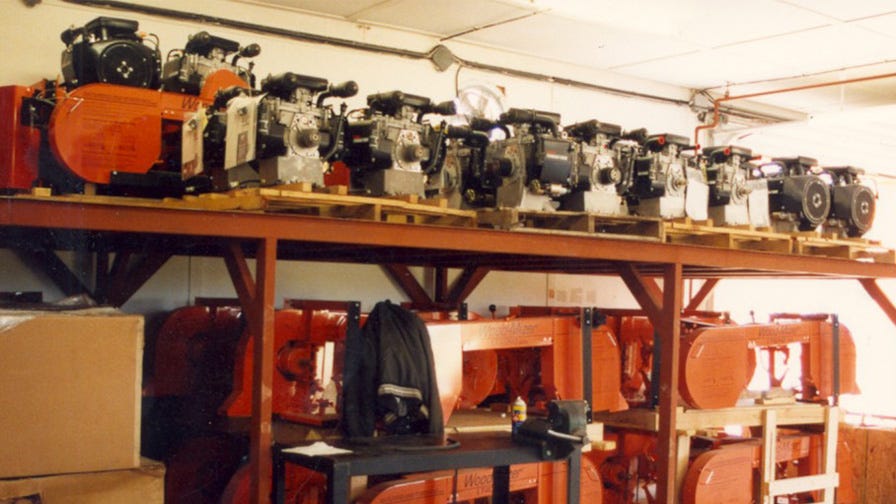
Currently, in the offering
The Wood-Mizer LT40 sawmill is offered today in gasoline and electric versions in a few power options. The future owner can choose freely which power option would match their individual sawmilling needs and go for one of the electric versions 11, 15, and 18,5 kW, the Kohler gas engines 14-38 KM, or the Kubota diesel engine D25.
It is worth mentioning the exceptional drive transmission mechanism, which stands out from the rest of the sawmills in the series. It is separated from the blade chamber to protect it from the dirt and sawdust produced in the sawmilling process. The transmission of power from the main engine shaft onto the blade wheel is carried by a durable unified drive belt coupled with a clutch mechanism – either a standard manual clutch engaging the blade or an optional automatic clutch controlled electronically.
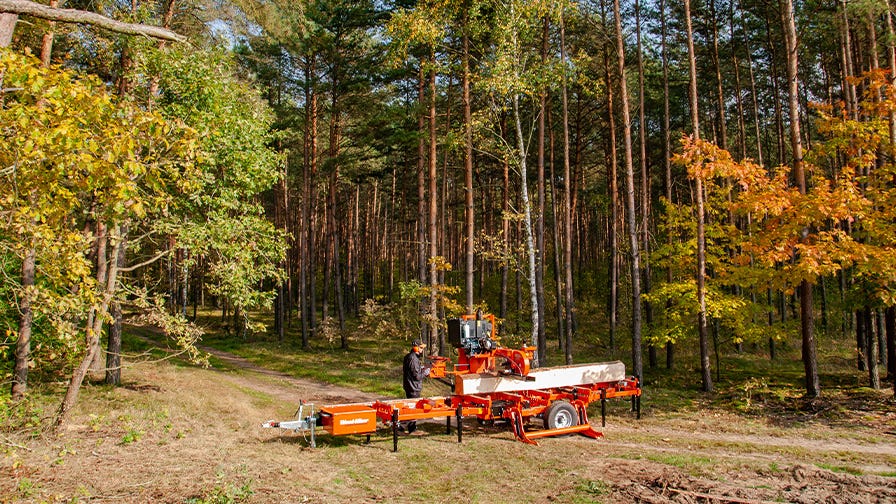
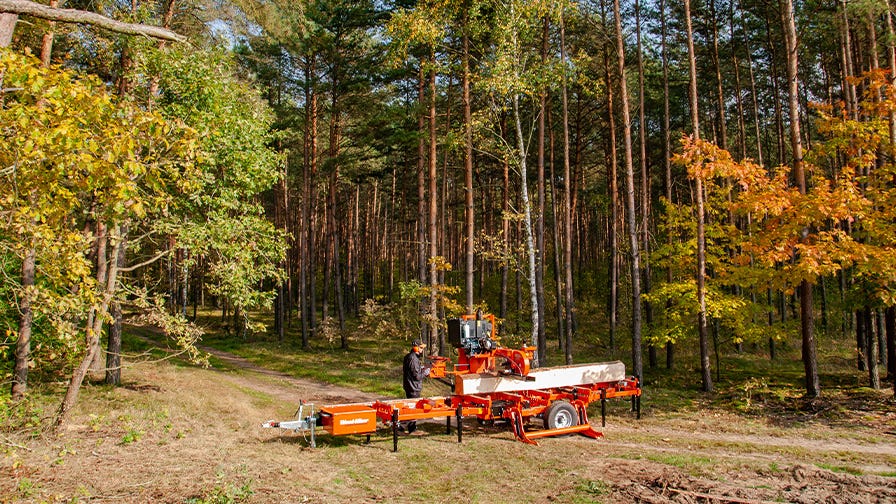
Read more from the series:
- Revolution on Two Wheels – The Birth of a New Sawmilling Technology
- The LT40 Sawmill History: Sawhead and Control Panel Upgrades
- The LT40 Sawmill History: Blades and Blade Guide System Upgrades
- The LT40 Sawmill History: Engine Upgrades
- The LT40 Sawmill History: Bed and Hydraulics Upgrades
- Wood-Mizer LT40: The Best Sawmill for Your Business
***